Getting to Know Brakes
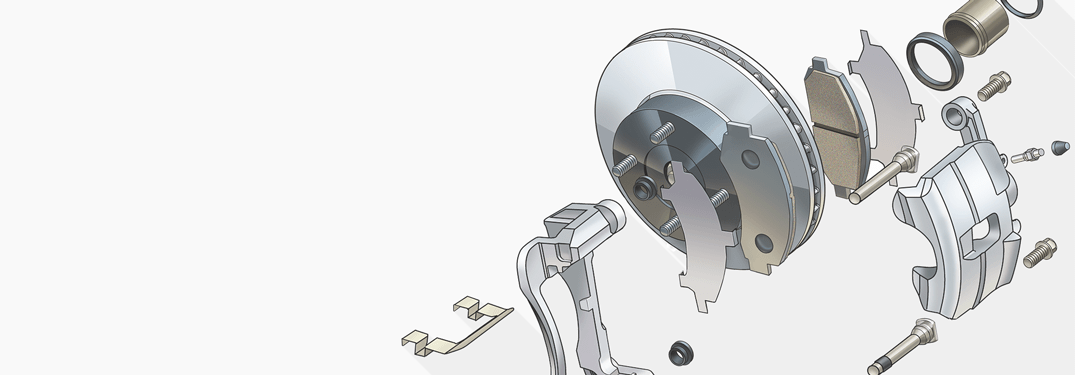
The three basic dynamic elements of an automobile are “go, stop, and turn.” Among these, the most important one related to safety is "stop." The "brake" bears this function of "stop." The brake “decelerates and stops” an automobile in motion. Furthermore, brakes also keep a parked automobile from moving (parking brake).
The "brake" is one of the most important safety-related components of an automobile, and is indispensable for realizing safety and security.
The brake decelerates and stops a moving automobile by changing kinetic-energy of the vehicle into thermal-energy and releasing it into the atmosphere.
It is the power of friction that changes kinetic-energy into a thermal-energy.
Friction is the resistive force which is generated when two moving objects make contact.
When the driver slams on the brakes at 100 km/h, there is enough heat generated to boil two liters of ice water (0 ℃) into hot boiling water (100 ℃) in three seconds.
Brakes are fitted to all four wheels of an automobile. The rotors or drums of the brakes rotate with the wheels, which are stopped with the power of friction. The strength of decelerating and stopping an automobile is called "braking force."
When the driver steps on the brake pedal, the power is amplified by the brake booster (servo system) and changed into hydraulic pressure (oil-pressure) by the master cylinder. The pressure reaches the brakes on the wheels via tubing filled with brake oil (brake fluid). The delivered pressure is about 30 times that of the driver’s stepping power. In other words, the strength of the driver’s foot at the brake pedal, which is about 15 kg, is amplified to about 450 kg of braking force.
There are various kinds of automobiles, such as fun-to-drive sports car, compact cars with high maneuverability, large-sized SUVs (Sports Utility Vehicles), and larger-sized trucks. These vehicles are equipped with either disc brakes or drum brakes based on their respective characters or usage.
On disc brakes, brake rotors are clamped by friction materials called as brake pads to stop an automobile.
Drum brakes have brake drums which rotate with the wheels. Each drum has brake linings which are pressed on the drums from the inside to stop the wheels.
Disc brakes and drum brakes each have their advantages and unique characteristics.
There are many different combinations of brake types used on automobiles. Some use disc brakes on all four wheels while others use drum brakes on each wheel. It is also not unusual to find automobiles using both types, such as discs at the front and drums for the rear wheels.
The basic requirements for brakes are twofold; sufficient braking force under all conditions, and stably generated braking force.
In addition to the basic requirements, reliable aspects including durability under repeated usage, adequate strength, optimum performance suited to the conditions under which they are used, are needed.
Moreover, brakes must also have high standards of qualitative appeal in addition to stopping performance. Demands for reassuring pedal feel, low level of noise and vibrations, and aesthetically appealing design are becoming stronger than ever.
Low cost of ownership is another important requirement. To this end, drag*1 and the weight of the brake components which impact fuel efficiency must be minimized. Friction material with a long service life is also important for reducing cost of ownership. From the manufacturer’s point of view, ease of production, serviceability and low production cost are also important.
Impact on the environment, such as reducing brake dust*2, is another task we take extremely seriously. At Akebono, various tests and development work are repeated constantly in order to meet these requirements.
Akebono develops and manufactures brakes for passenger cars as well as for various vehicles, such as rolling stock including “Shinkansen” bullet trains, conventional trains and subways, and also industrial machinery, such as fork lifts, and cranes.
Requirements for brake performances are diverse according to their usage. Depending on performance and cost requirements, the material, size and weight vary.
Disc brakes used for the front-wheel of an average passenger car are made of cast iron, and each weighs in at about 6 to 7 kilo-grams. On the other hand, in order to stop a vehicle that is faster or heavier, brakes that are bigger and weighs more are needed. The heaviest brake manufactured by Akebono is for large-sized dumper trucks used in construction sites. These heavy dumper trucks with wheel diameters of over three meters use brakes that weigh more than 120 kilo-grams each. It takes at least four adults to lift one of these brakes.
Brakes for motorcycles are comparatively lightweight at about 600 grams each for an average two-wheeler. This means, the brakes for a heavy dumper truck weighs about 200 times more than those of a motorcycle. In order to realize enough braking force to stop a heavy vehicle like this dumper truck, safely and consistently, a heavy brake like this is necessary.
However, it is not sufficient to simply make a brake heavier to increase stopping power and braking force.
Weight saving is an important requirement for the sake of improving fuel consumption and minimizing environmental impact. Technologies for reducing weight while maintaining the required rigidity is indispensable when developing and manufacturing brakes. This is especially true for vehicles for motorsports. Brakes are exposed to extraordinary speeds, but at the same time the components must be as lightweight and compact as possible.
Akebono develops and builds its products to cater to the customer’s needs.
The phenomena called "noise" and "vibration" spoil the pleasant ride of an automobile. They are the squealing noise and vibrations which the drivers sometimes hear or feel when they apply the brakes. The technologies for improving comfort of the drivers and passengers by minimizing these unpleasant phenomena are called "NVH suppression technologies."
NVH stands for Noise (squeal), Vibration, and Harshness (vibrations generated by irregularities of road-surfaces). Imagine tracing the rim of a wineglass containing water with a wet finger. The glass resonates (resonance) and a sound (squeal) is generated. Vibrations are generated by the friction caused by the finger tracing the wineglass, which in turn resonates with the glass containing water, thus producing a sound as in a musical instrument. The same principle applies to squealing noise and vibration. Vibrations generated by the friction between the pads and rotors are transmitted to the brake calipers, and the entire brake system resonates to produce a squealing noise.
There are many factors that must be considered to suppress squealing noise and vibration, including the material and shape of the components that resonate, driving environment, travelling speed, brake temperature, and so forth.
Controlling squeal noise and vibration are very important design criteria when developing a brake system.
At Akebono, NVH suppression is one of the key technologies for producing a better brake.