Initiatives in Production
Initiatives to Reduce CO2 Emissions and Water Usage
Akebono Brake Group has been promoting an energy and CO2 reduction project since fiscal 2007, improving onsite facilities at all sites to help reduce CO2 emissions and implementing energy conservation activities. Considering the importance of managing water to reduce usage, we have ascertained our water usage and continue to prioritize activities to reduce this.
Akebono Brake Group's CO2 emission volume worldwide in fiscal 2023 decreased by approximately 7,000 tons from the previous fiscal year to a total of 179,000 tons-CO2 due to consolidation of production processes and reduction activities of standby power . Our water usage decreased from the previous fiscal year by 20,000 m3 to 1,040,000m3.
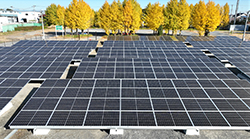
In addition, solar power generation using on-site PPA at Ai-City, headquarters has been in operation since January 2024, and is expected to reduce CO2 emissions by 106 t-CO2/year.
Akebono will continue activities to reduce CO2 emissions and water usage in the next fiscal year.
Total CO2 Emission and CO2 Emissions per Sales (Akebono Brake Group Worldwide)
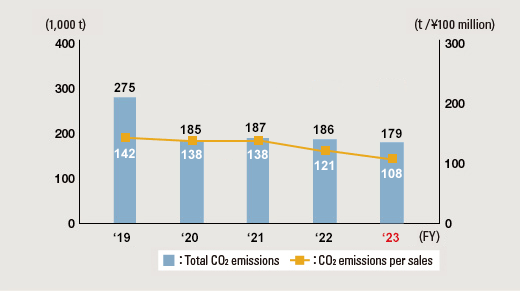
Water Usage and Water Usage per Sales (Akebono Brake Group Worldwide)
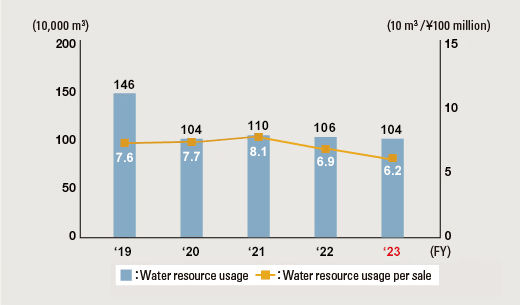
Continuation and Improvement of Zero Emission Initiatives
In order to eliminate waste material generated by our business, Akebono Brake Group continuously promotes zero emission initiatives. In 2004, we achieved our goal of no landfill disposal of industrial waste in our main domestic locations. Zero emission goals promoted by Akebono (no direct landfill disposal or incineration) was achieved by all Akebono Brake manufacturing sites in 2007, marking the successful implementation of the zero emission plan in all our facilities.
Akebono Brake Group will keep contributing to the creation of a recycling-oriented society and will continue the research in efficient usage of recycled resources as well as reduction of waste disposal costs and optimization of disposal methods. In addition, we keep strengthening our efforts to achieve the goal of no emissions while further promoting “reduce, reuse, recycle” - the basic objective behind the zero emission concept.
Waste Generated in Fiscal 2023 (primary operations in Japan)
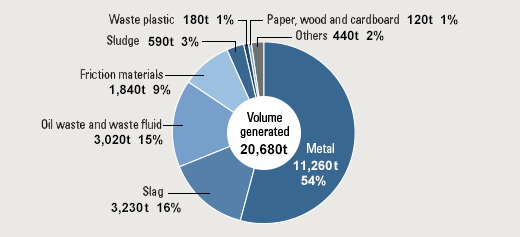
Fiscal 2023 Volume of Waste Generated and Recycling Ratio (major operations in Japan)
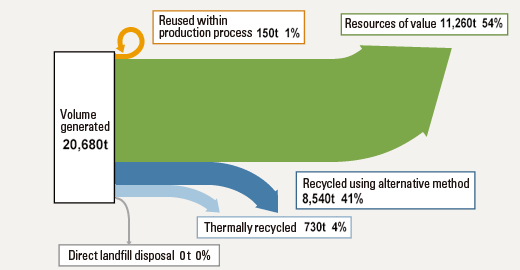
- * Since fiscal 2007, we eliminated landfill waste completely.
Change in Total Volume of Waste Generated and Total Volume Generated per Sales (major operations in Japan)
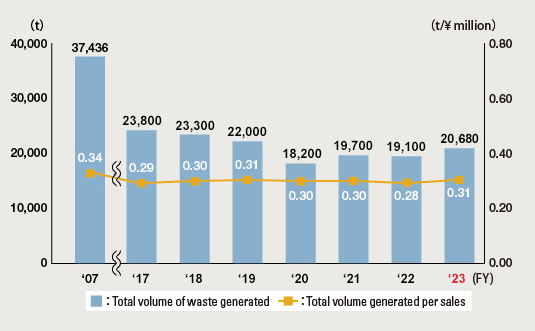
- * Total volume of waste generated includes resources of value, such as metals.
- * The right axis is the figure obtained by dividing the total generated volume (major operations in Japan) by domestic sales.
SQDC+E* Improvement Activities
Since fiscal 2019, we have been engaged in "SQDC activities" to ensure safety and quality while working to meet delivery time and reduce costs. We have added "E: Environment" to these approaches to make them "SQDC+E Improvement Activities" since fiscal 2022, and are also focusing on environmental activities such as SDGs and carbon neutrality. Based on the "5-Gen** attitude, monthly follow-up meetings are held at each plant in Japan as one of the activities related to C, "Cost," and improvements are promoted focusing on problems from the production floor.
In the follow-up meetings, people from other divisions also participate to share their problems and cooperate with each other to solve problems that cannot be solved by Manufacturing Division alone, leading to company-wide improvement activities.
One of the aims of our activities is to develop human resources who can solve problems through a sequence of processes and who can carry out their work from the bottom up.
* SQDC+E ... S: Safety, Q: Quality, D: Delivery, C: Cost, E: Environment
** 5-Gen ... Genchi, Genbutsu, Gennin, Genri, Gensoku: Go to the actual place, see the actual things and confirm the actual facts. Then take action based on fundamental theory according to decided principles.
Introduction and enhancement of Wastewater Treatment Systems
Akebono Brake Group has introduced and enhanced wastewater treatment systems and is carrying out environment-friendly production activities.
In fiscal 2020, Guangzhou, China achieved certification by the Environmental Impact Assessment Agency (EIA) after meeting strict effluent standards with the introduction of a new wastewater discharge station. In addition, in fiscal 2021, an online water quality monitoring system for wastewater outlets will be put into operation to further improve environmental maintenance management.
In fiscal 2020, Suzhou, China introduced automatic water quality measuring equipment and an online wastewater measurement system to strengthen wastewater treatment management, and in fiscal 2021, installed wastewater vacuum evaporation and drying equipment and modified the water quality control tank to comply with voluntary standards that are stricter than legal requirements.
Establishment of a production line that takes sustainability into consideration of manpower and goods
The Production Engineering Department is aiming for "reusable design," "design with high material yield," "design with low energy consumption," and "design with consideration of environmental impact” when designing production equipment and jigs and tools.
1. manpower saving through automation
We are focusing on promoting automation of production lines. In addition to anticipating a future shortage of human resources, we are contributing to the reduction of energy consumption for lighting, air conditioning, etc. through labor savings.
2. high-yield production line design
We are working to improve material yields in machining and casting processes through the use of CAE. We are also working to reduce energy consumption by establishing high-operation-rate lines that do not produce defective products.
Most recently, we have been working to reduce the amount of cutting oil carried off the machine due to the oil adhered to product, etc., and are contributing to the environment and safety by reducing the frequency of cutting oil refills and preventing oil from dripping onto floor surfaces.
3. Other steady activities
- Reduction of energy consumption by electrification of actuators and selection and adoption of energy-saving and high-efficiency equipment
- Reduction of CO2 emissions through on-line production preparation support
- Energy saving in facilities (mainly in casting and painting processes) through the use of highly heat insulated materials