摩擦材
ブレーキパッド、ブレーキライニング
ディスクブレーキやドラムブレーキには、それぞれブレーキパッドやブレーキライニングと呼ばれる摩擦材が装着されています。
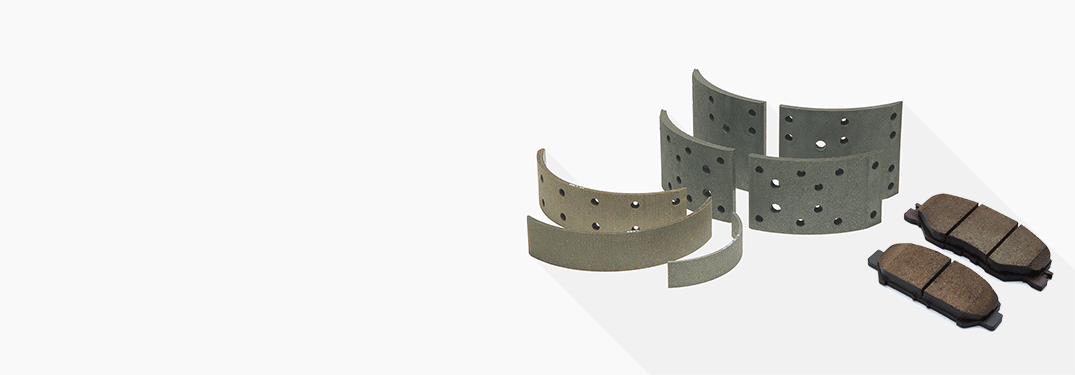
ディスクブレーキやドラムブレーキには、それぞれブレーキパッドやブレーキライニングと呼ばれる摩擦材が装着されています。
ディスクブレーキやドラムブレーキには、それぞれブレーキパッドやブレーキライニングと呼ばれる摩擦材が装着されています。
ディスクブレーキやドラムブレーキには、それぞれブレーキパッドやブレーキライニングと呼ばれる摩擦材が装着されています。
摩擦の力で制動する(減速・停止させる)仕組みのブレーキにとって、摩擦材は重要な役割を担っています。
ブレーキパッドやブレーキライニングは、10~20種類もの原材料を配合してつくります。求められる条件・性能に応じて、原材料をどのように混ぜ合わせるかは大変難しく、ノウハウが必要となる、akebonoが誇る技術です。
製造方法によっても、摩擦材の品質は大きく変化します。akebonoは、長年培った開発・製造の技術により、お客様のニーズに応える、高性能・高品質な摩擦材を提供しています。
ディスクブレーキパッドやドラムブレーキライニングは、10~20種類の原材料を配合してつくります。配合する原材料は、それぞれの役割から「結合材」「補強材」「摩擦調整材」の3つに分けられます。
結合材は、原材料を固めて強度を確保する役割があります。現在では、主にフェノール樹脂が用いられています。
補強材は、摩擦材の強度を確保する役割があります。アラミド繊維や金属繊維など、各種の有機・無機繊維が用いられます。
摩擦調整材は、主に摩擦材の効きの強さを調整する役割があります。効きの強さを向上させたり、安定させたりするためのものです。潤滑剤、有機充填材、無機充填材、研削材、金属粉などさまざまな原材料が必要に応じて配合されます。
これらの原材料の配合の違いや製造方法の違いにより、摩擦材はいくつかの種類に分けられます。
摩擦材には、適切な効きの強さが求められます。摩擦材の効きは、摩擦力の強さ、滑りにくさを示す摩擦係数「μ(ミュー)」で表されます。
さらに、走行速度や車両重量、ブレーキの使用による温度変化などの使用条件や、湿度、水、泥などの影響といった環境条件に対して、常に安定した効き(効きの具合の変化が少ないこと)を発揮することが求められます。また、熱に対する強度や機械的な強度が十分にあることも重要です。
使用とともに摩耗する摩擦材は、耐久性の高さも重要となります。また、ブレーキをかけたときに、鳴き・異音・振動を発生させにくいことも、求められる重要な条件です。さらに、摩擦材が接触する相手材であるディスクローターなどに、損傷を与えにくいものでなければなりません。ブレーキやブレーキオイルの温度が上がり過ぎないように、摩擦材には熱伝導率が低いことも求められます。
摩擦材に求められる主な性能
akebonoでは自動車や新幹線、また、モータースポーツ用の高性能車向けまで、幅広いブレーキパッド・ブレーキライニングを開発・製造しています。新幹線など高温・高負荷の条件でも強度を発揮する必要がある場合は「金属系」の摩擦材、また、高速からブレーキをかけることが多い、主に欧州地域向けには「ロースチール」の摩擦材など、用途によってさまざまな種類が使い分けられます。
乗用車向けには、効き、強度、鳴きにくさなどを高い次元でバランスすることができる「ノンスチール」のブレーキパッドが主に使用されています。「ノンスチール」のブレーキパッドは、akebonoの主力製品です。
akebonoは、常に最先端の技術を習得することを目的として、高性能ブレーキの開発を継続しています。akebonoの高性能ブレーキは、さまざまなモータースポーツ用車両に供給されており、このような極限の世界で得られたノウハウが、一般の乗用車向けブレーキパッドやブレーキライニングの開発にも活かされています。
ニュルブルクリンク24時間耐久レース用
ブレーキパッド
高性能量販車用 10ポット
ブレーキパッド
高性能量販車用 6ポット
ブレーキパッド
摩擦材の開発では、さまざまな原材料の組み合わせ方や、製造条件の最適化によって、性能はもちろんのこと、長期にわたっての使用に耐えうる品質の確保が求められます。お客様のお手元に製品をお届けするまでには、摩擦材単体の物理・化学特性評価、ダイナモメーターと呼ばれる実際のブレーキを装着することができる試験機による摩擦特性評価、実車による車両適用評価など、短いものでも数ヶ月、長いものだと数年をかけた開発が行われます。さらには環境保全にこだわった原材料の開発にも取り組んでいます。
akebonoでは開発の初期に必要な基礎特性の評価から、実車の評価までを実施できる設備を自社内に備え、お客様に満足いただける性能・品質を確実に提供し、摩擦材に関するエキスパートとして、日夜、研鑽を続けています。
摩擦材は、多くの製造工程と検査・試験工程を経て、製造されています。
多くの性能が求められる摩擦材の開発において、原材料をどのように配合するかは非常に重要な技術のひとつです。また、つくり方でも品質が変化してしまうため、製造技術も重要となります。akebonoは、長年培った経験に基づく開発技術、製造技術により、常に安定した性能・品質のディスクブレーキパッドを提供しています。
摩擦材の検査・試験工程では、摩擦材の硬さや強度などの物理特性評価から、有機系材料の化学分析など、さまざまな手法を用いて、摩擦材の品質の確認を行っています。効きや摩耗、鳴きなどを試験するためには、実際のブレーキを装着して試験をすることができる、ダイナモメーターと呼ばれる試験機を用いて試験を行います。
また、akebonoでは、お客様の視点に立った摩擦材の試験を実施するために、数多くの評価路・評価設備を備えた、自動車部品メーカーのテストコースとしては国内最大規模を誇るテストコース「Ai-Ring(アイ・リンク)」で評価試験を行っています。
テストコース「Ai-Ring」では、台上評価から実車評価まで、さまざまなブレーキ評価試験を行うことができます。
摩擦材の開発・製造を続けてきた長い歴史の中で、akebonoは常に「安全・安心」というテーマに真摯に取り組んできました。
2000年頃まで、一般的に摩擦材の原材料として、耐熱性に優れるなど高い性能を発揮するアスベストが使用されていましたが、1970年代に海外でアスベストの健康に対する影響が報告されたことを受け、akebonoは1970年代に日本の企業の中でもいち早くノンアスベスト製品の開発を始めました。他社に先駆け、1992年には乗用車OEM(新車組付け)用の全製品を、1994年には商用車OEM用の全製品をノンアスベスト製品に切り替え、2000年以降は補修部品においてもアスベスト製品の生産を全面的に中止しています。
また、これまで摩擦材には、高温時の効きの安定性のために銅が使用されてきましたが、銅の環境規制の動きを受けて、銅フリー摩擦材*の開発・製造に取り組み、補修用としては2007年から、新車装着用としては2014年から、銅フリー摩擦材をお客様に納入しています。さらに、akebonoでは、次世代の技術として、植物資源(バイオマス)を活用したブレーキパッドや、摩耗粉を発生しないブレーキパッドの開発にも取り組んでいます。